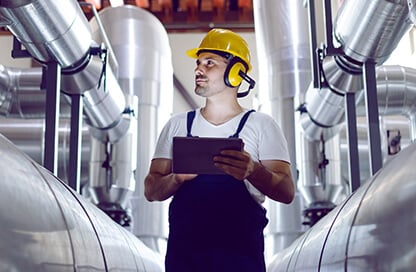
Boosting asset reliability starts with increasing consistency. You need to make sure the maintenance team’s doing the right work the right way.
And checklists, backed by the right equipment maintenance software, are a fast way to see concrete results.
First, let’s lay a strong foundation with some important definitions.
What is an equipment inspection checklist form?
Maintenance professionals call them many different names, including heavy equipment inspection checklists, construction equipment inspection forms, equipment inspection forms, preventive maintenance checklists, and equipment maintenance inspection checklists.
But for all the different names, they’re all roughly the same.
On the most basic level, a checklist is a list of things to check. We can get more expansive and say it’s an ordered list of tasks someone needs to perform before a specific action takes place. The goal of the list is to ensure that end action is justified.
The classic example is the preflight checks pilots perform before takeoff. They have a list of tasks they must successfully complete to ensure it’s safe to fly. Some of the items are visual inspections. Others require them to manipulate the aircraft.
For example:
- Master Switch – ON
- Flaps – DOWN
- Fuel Quantity Indicator – CHECK
- Master Switch – OFF
Notice how they have to turn the master switch on before checking the flaps and fuel? That’s an important part of the definition of a checklist. It’s not just a list of tasks; those tasks are in a specific order.
Preflight checks are a type of pre-use checklist. The goal is to confirm that the plane is safe to fly. There are other types, though, including maintenance checklists. They work the same way, but the goal is to confirm the asset or equipment is in good working order and doesn’t require repairs.
What are the benefits of a good inspection checklist?
Checklists create consistency, and there’re a lot of benefits from being consistent.
Maintenance techs do inspections completely, properly
Pilots started using checklists because planes are complex machines with a lot of moving parts. There’s too much to safely remember, no matter how much experience a pilot might have. In fact, experience might work against the pilots as they become overconfident and complacent over time.
It’s the same with maintenance technicians. The assets and equipment they need to maintain are complex and have a lot of moving parts. There’s no way for them to remember everything.
In fact, pilots likely have it easier than your techs. They tend to focus on one type of aircraft, often one specific model. Techs have a lot of different equipment they need to master. Also, pilots likely fly the same plane more often. Techs might work on an asset and then not have to look at it again for weeks.
Maintenance techs learn how to complete inspections faster
Adding checklists to your workflows also makes it easier to train new technicians. The age-old tradition of having a master and apprentice is a time-honored system for training in the trades. People learn by working under the direct supervision of someone more experienced. But with checklists, you can speed this process along, setting up junior techs to work independently sooner. The checklist tells them what tasks they need to complete.
Maintenance managers protect the whole organization
Checklists are a great way to make sure things are done right. But they’re also helpful when things go wrong.
When techs do every inspection the same way, it’s a lot easier to track down process-related problems and fix them. The reason is that there are fewer variables to investigate. For example, if every tech is checking and changing the lubricant according to the checklist and schedule, but you still have issues with excess heat from friction, you know you need to change lubricants.
And if there are ever any questions about compliance with government regulators, a solid record of checklists proves your good faith efforts to meet the standards.
How can you tell if a checklist is any good?
By working backward from the benefits you should be seeing, you can judge a checklist’s effectiveness.
Ask yourself:
- Are new techs learning the ropes faster, able to work independently sooner?
- Are techs working more consistently during inspections?
- Are techs catching more issues before they have a chance to grow into big problems?
- Am I collecting proof that I’m in line with current best practices and regulations?
If you can answer yes, there’s a good chance your checklists are working.
How can you develop new maintenance inspection checklists or improve existing ones?
It’s a multi-step, iterative process. It’s also a bit of a team effort.
Collect existing asset documentation
For new checklists, you can start by collecting everything you already have on that asset or piece of equipment, including historical maintenance and repairs histories, O&M manuals, and warranties. The warranties are a good idea because there might be something you need to include on the checklist to avoid voiding the coverage. The manuals tell you what the manufacture recommends, while your own work order records give you a clear picture of past problems you want to avoid.
Also, make sure to reach out to the manufacturer to find out if there have been any recalls or updates. You want to make sure you aren’t missing any new developments older manuals don’t cover.
Talk with your maintenance techs
If all your department’s hard-won maintenance know-how is locked up in your senior techs’ heads, you’re running a lot of “key person” risk, which means all that knowledge can easily walk right out the door when those techs transfer or retire. It’s always a good idea to get as much of that tribal knowledge somewhere safe before you lose it, and creating checklists is one way to do it.
Because your techs know the assets and equipment well, they already have a good idea of how best to take care of them, what to look for, when to be worried, and when everything looks fine. When developing checklists, you can use anything from informal conversations to a formal sit-down meeting to get their insights down.
Organize for both location on the asset and asset’s location
Once you know the steps, you need to put them in order. Try to organize everything logically, based on where things are in the asset. If you were creating a checklist for a vehicle engine, start at the front and work your way back. Check the radiator and the fan. Then move to the battery followed by the oil and windshield washer fluid. Next, look at the air filter.
Think about where parts are in the asset. Then think about where the asset is. You might have two similar assets but with different checklists, one for each location. An air compressor on your factory floor needs a different checklist than the same model located outside the building, exposed to the elements.
Think about safety all the way through
Make sure the checklist starts with instructions on how to safely lock out and tag out the asset or equipment, which is different than just turning it off.
Generally, locking out equipment involves four steps:
- Identify all energy sources connected to where you’re inspecting.
- Disable, redirect, or stop all that energy
- Apply purpose-built devices to prevent anyone from starting it up.
- Confirm that the asset is at a state of zero energy.
Make sure the checklist ends with instructions on how to put everything back together safely. If techs have to open panels to access the equipment, there needs to be instructions on how to replace and secure them. Often, the last step of a maintenance inspection involves starting up the asset or equipment to ensure everything is back where it needs to be.
One more thing: if your checklist is too long, it might not be safe. Why? Because once you get past a certain length, you run the risk of techs “pencil whipping” the checklist, rushing through because that’s the only way to get the inspection done without taking a ton of time. So, make sure you include everything on the checklist you need but nothing you don’t need.
What types of equipment should be on your inspection checklist?
The answer depends on your industry. Let’s go through some of the more common examples.
Equipment types for inspection
Heavy or powered equipment
Mechanical equipment
Non mechanical equipment
Here they are in a bit more detail.
Heavy or powered equipment inspection checklist
Assets and equipment include:
- Forklift
- Scissor lift
- Crane
- Bulldozer
Examples of things to check and do include:
Check oil level and discoloration
Inspect tires for worn tread, crakes, proper inflation
Remove and inspect air filter
Mechanical equipment inspection checklist
Assets and equipment include:
- Pump
- Air compressor
- Conveyor belt
- Extruder
- Refrigeration units
Examples of things to check and do include:
Check extruder screw for chips and wear
Check all air tubing for cracks and leaks
Inspect seals and fix leaks
Non mechanical equipment inspection checklist
Assets and equipment include:
- Plumbing
- HVAC
- Gas lines
- Electric panels
Examples of things to check and do include:
Clean all drains and p-traps
Check condensate drain
Ensure breakers are secure
Why should you use an equipment inspection checklist built into CMMS software?
Because it makes everything so much easier. It supports and simplifies every step of the process, from developing checklists to sharing them with the team, from making sure they’re current to updating them.
If you already have a CMMS up and running, you already have a lot of the information you need collected and protected in your cloud-based, always accessible database.
From inside the preventive maintenance software, you can create checklist templates that you can then add to any on-demand or preventive maintenance work order in just a few clicks. Need to update the items on the list? As soon as you’ve updated the template, every new work order you generate contains the new information. Because everything is done in one spot, you only have to make changes once. The CMMS takes care of all the boring repetitive work for you, and that means fewer mistakes and bad data in the system. Remember, boring, repetitive tasks are where people make all lots of little mistakes.
Executive Summary
Inspections are a critical for setting up and running a successful preventive maintenance program. And at the heart of maintenance inspections is your equipment inspection checklist, an ordered list of things to look for and do prior to confirming an asset is ready to go.
Checklists deliver increased consistency so techs can learn the ropes faster and find problems sooner. A good checklist has everything in a logical order and focuses on safety throughout.
And a good CMMS makes the whole process of working with maintenance checklists, from development to deployment, a whole lot easier.