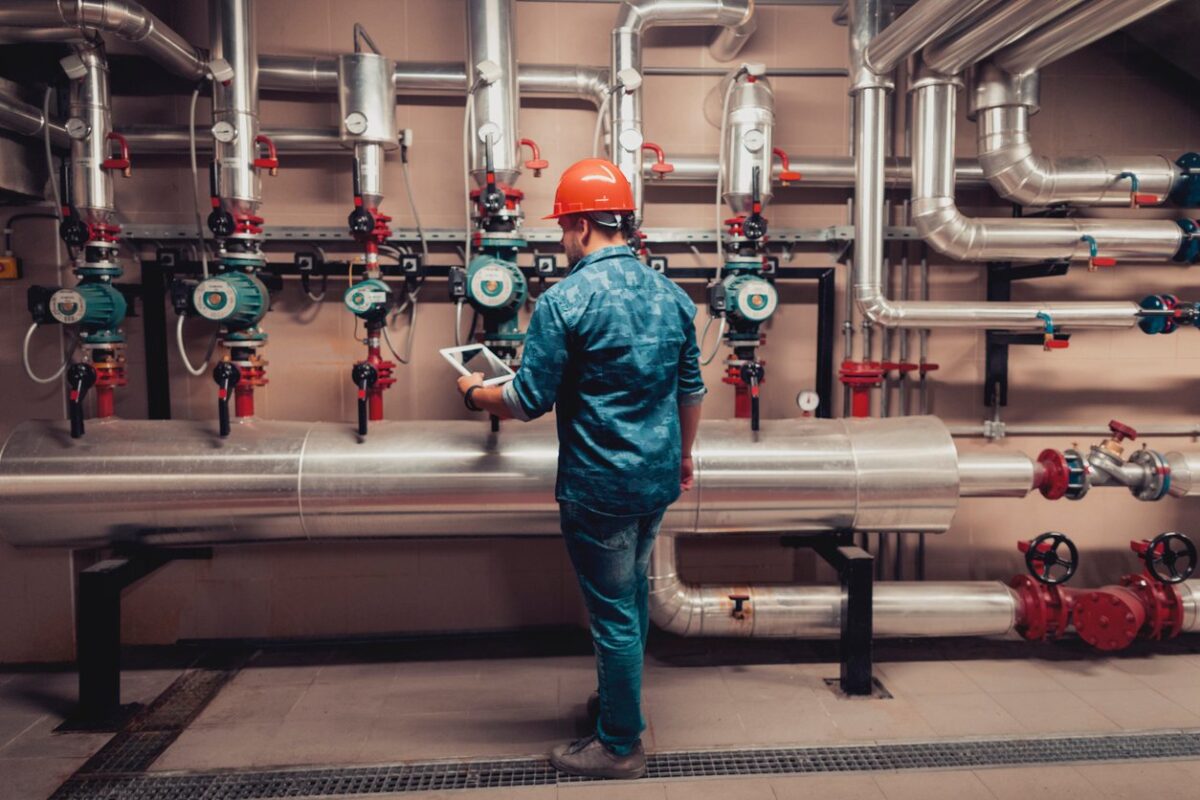
Although shutdown maintenance can be a complex project, the idea behind it is simple. There are some maintenance inspections and tasks you can only do when your facility is shut down. It’s like when you’re changing the engine oil or fixing a flat, where the first step is stopping the car. And even though you’re losing time on the road, you’re gaining a lot in efficiency, completeness, and safety.
What is shutdown maintenance?
Shutdown maintenance is the collection of inspections and tasks the maintenance team carries out when an entire facility is shut down specifically to facilitate this work.
Depending on the industry and location, other common names are “maintenance turnaround” and “maintenance stoppage.” But the main idea is always the same: A facility is shut down specifically for the maintenance team to perform inspections and tasks they can’t do when the facility is up and running.
How can you plan shutdown maintenance?
To get the most maintenance out of the shortest possible turnaround, you need to invest in a lot of planning and preparation. Although there’s no perfect formula for maintenance turnarounds, you can follow these five steps to get and stay organized.
Set scope
Here, you’re trying to answer a lot of “what” questions, including which assets and equipment you need to cover. You also need to think about what you hope to do with each. For example, for some you might be testing and inspecting, while for others, repairing and replacing. Make sure to prioritize work that you can only do during a shutdown. If it’s something the team can close out during normal operations, it makes sense to leave it off the list.
It’s critical that you match all these decisions to a defined set of organizational goals, including key performance indicators for:
- Safety
- Cost
- Reliability
- Availability
It often helps you start with your goals and work backwards from there, increasing the scope only as much as you need to meet them.
Plan work
Now you’re looking at the “how” of the turnaround, which means you’re developing inspections and tasks, and making sure you’re set to have the parts and materials you need to close out the work properly. If you’re planning a lot of inspections, you need to confirm you have the right tools to do them.
When looking for inspections and tasks to include, make sure to reach out to the manufacturers of all your major assets and equipment to check for recalls and updates.
Schedule everything
It’s important to also consider the order you’re scheduling the team to complete the work. You need to estimate how much time they need for each, and schedule accordingly. Make sure to add in time to review all the work, too.
One thing you can absolutely count on is the unexpected, so you need to add some time and resource padding into your scheduling.
Shut down
Once you have it all scoped, planned, and scheduled, it’s time to do the actual work.
Make sure to keep track of all the times the team makes changes to your original plans. If something took longer than you had expected, or needed different parts and materials, make a note. You can leverage everything you learn from this shutdown to future projects.
Look back
Turning mistakes into lessons requires a formal process. At the final stage, you’re looking back, but you’re doing it as a way of looking forward. Once you’ve reviewed all the work the team did and gone over what went well and what didn’t, you’re in a better position to plan your next turnaround.
Start by asking yourself:
- Was the objective and scope of the shutdown clearly defined?
- Were there deviations in your schedule or budget? If so, why?
- Did you optimize your shutdown time? Were there other maintenance tasks you could have accomplished?
- Did the shutdown team communicate well with its members and others involved in the process?
- Were there any issues that occurred while bringing your equipment back online?
Honest answers truly help you be better prepared for future shutdowns.
How can you bring assets and equipment back online after a shutdown?
Just as important as the shutdown and maintenance work is getting everything back online. It can be stressful because of potential costs and safety concerns.
Check for hidden health and safety hazards
When a shutdown lasts for more than a few weeks, you need to consider additional safety measures before reopening. There could be microbial hazards, such as mold or unsafe water due to pipe corrosion or chemical by-products.
The Centers for Disease Control and Prevention, for example, has issued guidelines for avoiding these hidden hazards, including:
- Maintaining low indoor humidity, not exceeding 50%, to prevent mold
- Operating your HVAC system for at least 48 to 72 hours as a flush-out period before returning to service
- Continuing to check your HVAC system, including air filters, after reopening to ensure it’s operating efficiently
It’s important to consider other environmental conditions, including ambient temperatures, before restarting equipment.
Follow return-to-service inspection checklists
When bringing your equipment online again, you need to be clear on the sequence of steps to follow. Some systems may have tight dependencies and prerequisites. For instance, raw material production must start first before upstream production. And some systems require fixed environmental parameters. For instance, you need to verify the electrical and plumbing configurations meet all specifications.
Failing to follow the prescribed sequence for bringing equipment back online can lead to a series of failures that can be hard to recover from quickly, delaying your return to service. This is why having an inspection checklist is crucial.
Sometimes re-opening and servicing your equipment can inadvertently lead to misalignments or other issues. Your inspection list should be as detailed as possible, helping the team review every individual asset to ensure overall readiness. To create a practical and relevant inspection list, look for ways to combine the equipment manufacturer’s manual with your technicians’ hands-on experience.
Ideally, your inspection checklist should be in a digital format technicians can access from anywhere. They should use it to check factors that could indicate a potential failure, such as noise, leaks, and unexpected changes in temperature.
How does asset management software help you with shutdown maintenance?
Modern asset and facility management solutions can help you at every step. The reason is because it has all your data in one safe spot, where it’s also secure and accessible.
When you’re first deciding which assets and equipment to include, you can look at the master asset list inside the software. From there, you can review all the associated work orders, giving you a sense of where you should focus your efforts. But reviewing historical work orders doesn’t mean clicking through them one at a time; instead, you can use the software to autogenerate reports for key insights into your operations.
From there, you can use the platform to set up and schedule all your inspections and tasks, the same way you would use it day-to-day for both preventive maintenance scheduling and on-demand work order generation.