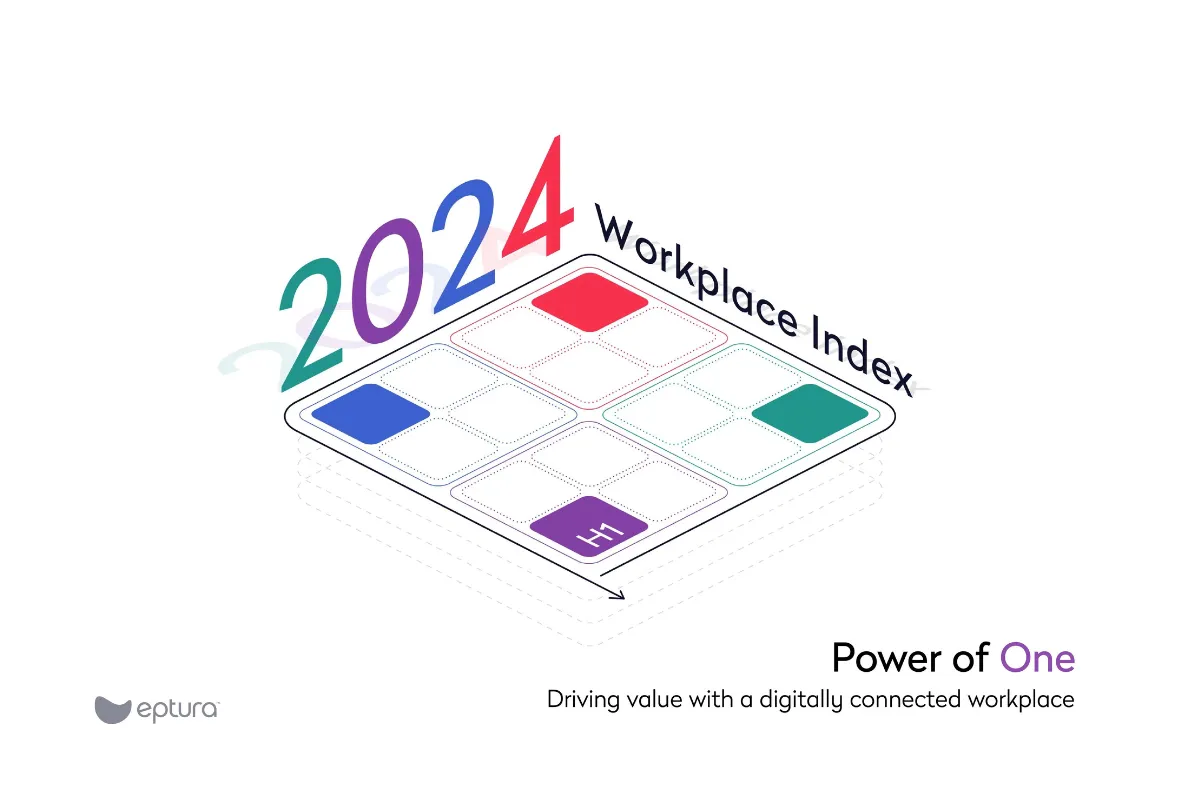
New propriety research from Eptura reveals a four-stage model of implementing worktech solutions. The value of this new model is descriptive and prescriptive. First, workplace and operational leaders can now establish their current location, giving them a realistic picture of past progress and future possibilities. Then, by understanding the challenges, goals, and near-future planning common to each stage, they can begin to confidently chart their route to greater collaboration, reduced operational costs, and increased asset revenue.
Eptura’s H1 2024 Workplace Index incorporates independent research on enterprise companies across North America, Europe, and Asia Pacific, with insights from C-level, vice-president, and country-head leaders across departments, and leverages anonymous user data from more than 5,000 companies, including 19,000 buildings, 95.5 million desk bookings, and 25 million room bookings.
Digital connection evolves in four stages
Based on conversations with workplace and operations leaders, Eptura developed a four-stage model to describe how an organization moves toward a connected workplace.
Stage 1 is the initial jump from manual methods to a single point digital solution. For example, you might go from a paper-based visitors log to a stand-alone digital visitor management system. Or you could move the preventive maintenance schedule from email-attachment spreadsheets to a dedicated software solution. Although there are operational efficiencies — it’s now easier to capture data and harder to lose it — you’re not yet sharing data outside of set silos.
There’s more visibility, but the view is still narrow.
At Stage 2, organizations bundle multiple solutions from one vendor, cutting management and software costs. By Stage 3, they’re at a single platform that creates integrated use cases for cross-platform functionality, digital mapping of the workplace, and access to cross-functional data. By sharing data across workflows, organizations can discover new operational efficiencies.
The big picture is now coming into sharper focus, making it easier to spot opportunities for improvement and leverage data for better decision-making. You might be using occupancy data trends to schedule preventive maintenance inspections and tasks for times you know the offices are mostly empty, for example. Or using room booking data trends to help guide capital projects planning.
Stage 4 is when everything comes together across the enterprise with an integrated ecosystem delivering real-time predictive analysis and modeling backed by Internet of Things (IoT) asset communication and digital twins.
At the final evolution, organizations can leverage a smart, interconnected system to deliver optimal outcomes for facility, assets, and employee experience at all their spaces, across multiple locations.
Technology requirements change at each digital stage for asset management
Facility and maintenance professionals already know the basic benefits of moving from reactive to preventive maintenance. By finding and fixing small issues before they grow, you can cut overall costs by reducing unplanned downtime and increasing useful life cycles. When maintenance is planned and scheduled, technicians arrive onsite with the tools, time, and knowledge they need to close out quickly.
In fact, Eptura’s latest data reveals technicians require roughly twice as much time to complete reactive versus preventive work.
It’s easy to understand why. Much of reactive maintenance is “putting out fires,” and maintenance technicians must work under many of the same constraints as firefighters. Because they don’t know what they’re dealing with until they arrive on scene, they default to bringing too many tools and supplies. On scene, they’re making best guesses with limited visibility of fast changing facts.
But how they hope to implement or improve their ability to deliver preventive and predictive maintenance over the next 12 months depends on their digital stage.
Organizations at Stage 1 are most interested in delivering data analytics, likely because they have never had them before. Paper- and spreadsheet-based attempts to manage work orders are too scattered and too error prone to facilitate reliable reports. At this stage, there is also a lot of interest in supporting technicians with mobile apps, maximizing the utility of the newly captured data by making it easy for maintenance teams to access it from anywhere.
At the multiple digital stage, organizations were also interested in data analytics, but they showed more interest in integrated workplace platforms than mobile apps. In fact, only 11% of companies at this stage said they were interested in mobile apps, which was the same percentage as those in the ecosystem stage. It’s likely the number is low because they already have mobile apps implemented.
What the data suggests is that at later stages, companies are hoping to connect more groups and larger systems – and even assets. By the ecosystem stage, the two most important technologies are integrated workplace platforms and IoT, tied at 18%.
Digital stages also predict perceived challenges for connecting revenue-generating assets
When we spoke with operational and maintenance leaders, the most common answers to “What barriers do you face digitally connecting assets?” were:
- “We have siloed functions.”
- “Incomplete data to provide actionable insights.”
- “We don’t have the skilled labor.”
But digging deeper into the results reveals clear stage-based differences. Companies in Stage 1 worried most about siloed functions, while those in Stage 2 felt incomplete data was the biggest barrier. By Stage 4, companies are still worried about siloed and incomplete data, but were mostly unconcerned about skilled labor. In fact, companies in the first two stages were at 14%, while Stage 4 was at less than half, just 6%.
A possible explanation is that the process of moving through the digital stages involves acquiring increasingly skilled operations and maintenance professionals. So, by the time a company reaches Stage 4, they already have the human capital they know they need to get the most from their investments in an interconnected ecosystem for facility and workplace management.
Investing in people appears to play a part in reaching Stage 4, and companies at earlier digital stages now know they should anticipate and budget for training and upskilling as they evolve.
Perceived challenges remain the same at every stage for sustainability
The latest Workplace Index report also looked closely at how companies are dealing with ever-increasing sustainability requirements. Governments are setting aggressive goals, and organizations across industries need to quickly catch up.
For example, the U.S. government plans to create a “clean energy economy” through the following goals:
- Reducing U.S. greenhouse gas emissions 50-52% below 2005 levels in 2030
- Reaching 100% carbon pollution-free electricity by 2035
- Achieving a net-zero emissions economy by 2050
In the European Union (EU), the introduction of The Corporate Sustainability Reporting Directive means stricter sustainability reporting requirements to help “investors, civil society organizations, consumers and other stakeholders to evaluate the sustainability performance of companies, as part of the European green deal.”
Separate from government mandates, companies understand the ways environmental, social, and governance (ESG) initiatives can lead to:
- Top-line growth
- Cost control
- Productivity increases
- Investment optimization
However, unlike other areas in our report, here the self-reported challenges didn’t appear to change with the stages. For sustainability, the two main barriers were the economic climate and costs of technology. Companies didn’t feel they had the resources to invest in sustainability-centric technologies.
It’s possible some businesses may not be seeing the value of the systems they already have in front of them, and it’s because they’re drawing too hard a line between facility and maintenance management solutions and sustainability technologies.
Sustainability is closely tied to efficient, effective facility and maintenance management. At their core, every maintenance strategy is an attempt to reduce waste and to get the largest effect from the smallest effort. Preventive and predictive maintenance reduce costs, for example, by helping you avoid expensive labor- and parts-intensive repairs.
How enterprise leaders can apply lessons from Eptura’s digital movement model
Our data shows how challenges, aspirations, and near-future planning change at each of the four stages as an organization makes its way to a connected workplace. Equipped with this knowledge, companies are now in the best possible position to prepare. At Stage 1, for example, they can focus on the benefits of automated data capture. Because they know that data will live inside discrete workflows, they can make informed decisions about where to automate. For some, it will be visitor management. For others, space planning might be a higher priority.
And because even at Stage 1 they already have a clear picture of Stage 2, they’re motivated to get there. Once they arrive, the leadership also knows the types of technologies they’re most likely going to want to implement, which helps them streamline their selection processes, build institutional excitement, and manage expectations. The process repeats at every step.
“This report is designed to provide operational leaders with a map of the global worktech landscape,” explains Brandon Holden, CEO of Eptura.
“A map that can help every organization, wherever they are on their journey, take the next step towards a high-functioning workplace that reduces operational costs, enables greater collaboration, and increases asset revenue.”
Dive in. Download a copy of the latest Workplace Index report.