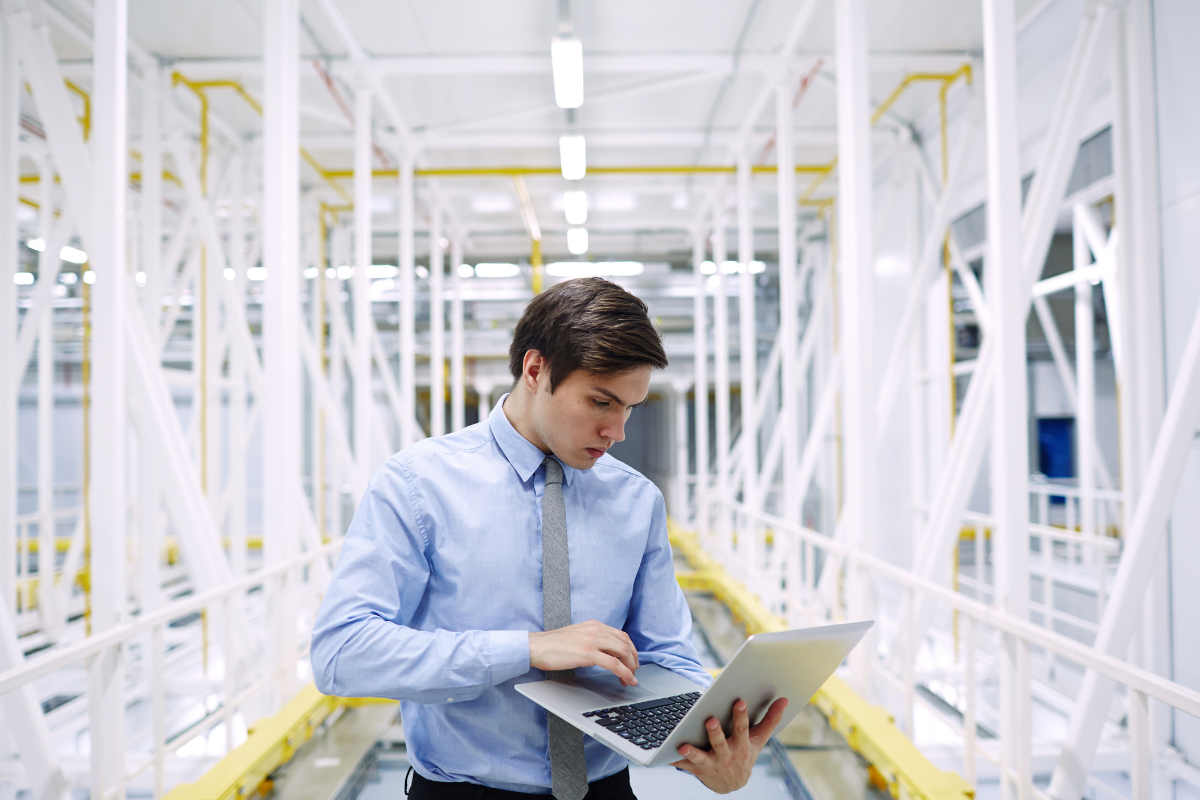
Facility retrofits can improve energy efficiency, safety, compliance, and overall operational effectiveness without the need for a complete rebuild or new construction. For example, a major retrofit at the Empire State Building reduced energy consumption by 38%, while also improving overall comfort for visitors. The retrofit at the Tate Modern Museum preserved the original structure while creating new galleries and, by including elevators and ramps, made the space more accessible. Retrofits can also focus on safety, like at Torre Reforma, one of the tallest buildings in Mexico, where a seismic retrofit helped meet stringent earthquake standards.
These projects are inherently complex, though, often involving multiple systems, assets, and equipment, as well as the teams that depend on and maintain them. By leveraging a system that connects building information modeling (BIM) with facility management (FM) workflows, organizations can significantly improve retrofit planning and execution. An integrated approach ensures that all stakeholders have access to accurate, up-to-date information, facilitating better decision-making, streamlined coordination, and more efficient project management.
What is BIM for FM?
BIM for FM integrates structured, multi-disciplinary data to create a digital twin, a comprehensive digital representation of a building. The model then serves as a centralized repository, providing detailed insights into systems, assets, and equipment. Facility managers can monitor asset performance, track maintenance schedules, and identify trends for better decision-making. BIM for FM ensures accurate, up-to-date information for effective planning and execution of maintenance and retrofit projects. It also streamlines workflows and improves communication among teams, optimizing capital project management by providing a clear overview of assets and their lifecycle, enabling better budgeting and resource allocation.
How can an organization leverage operations and repairs data for more effective retrofit planning?
When planning a retrofit, you can use existing maintenance and operations data captured through facility management workflows to support and improve planning.
By analyzing work order maintenance and repair histories, for example, you can find the areas or systems that frequently require maintenance or repairs and mark them as likely to benefit the most from a retrofit because addressing underlying issues can reduce future maintenance costs and improve reliability. For example, if the HVAC system in a particular building has a history of frequent breakdowns, it might be a high-priority candidate for an upgrade. In the same way, you can pinpoint high energy or water consumption areas by reviewing utility bills and usage data, indicating where upgrades to more efficient systems could deliver the greatest savings.
Understanding which parts of the building are most heavily used through occupancy and utilization data captured by the visitor management solution and room and desk booking features can help prioritize retrofits in areas that will have the most significant impact on user satisfaction and operational efficiency. For example, a large healthcare organization with multiple facilities can use this data to identify high-traffic patient care areas that may require upgrades to lighting, HVAC systems, and medical equipment. By focusing on these areas, the organization can enhance patient comfort and staff efficiency, leading to better healthcare outcomes and reduced maintenance costs. Similarly, a multinational corporation with numerous office buildings can leverage occupancy data to pinpoint frequently used meeting rooms and collaborative spaces. Retrofitting these areas with new and better audio-visual technology can boost employee productivity, ultimately driving higher business performance.
How can an organization leverage BIM data to support retrofits?
By integrating BIM with facility management solutions, organizations can gain a comprehensive understanding of their buildings, making retrofits more efficient, cost-effective, and safer.
Minimize downtime with precise planning
Retrofitting can cause disruption to daily operations like shutting down parts of the facility or restricting access to certain areas. Minimizing this disruption while ensuring the work is completed efficiently is important for maintaining productivity. A digital twin is a detailed, 3D model of the building created out of BIM data, allowing facility managers to visualize and plan the retrofit process with precision. This includes identifying the most efficient pathways for construction teams, scheduling work during off-peak hours, and coordinating with other maintenance activities to reduce downtime. They can also simulate the impact of different retrofit scenarios, helping to predict and mitigate potential disruptions.
By optimizing the retrofit plan, the team ensures that daily operations are minimally affected, maintaining productivity and employee satisfaction, and delivering cost savings by avoiding the need for temporary relocation or additional staffing.
Enhance safety with detailed simulations
Retrofitting can introduce safety and health risks, such as exposure to hazardous materials like asbestos and lead, or the creation of dust and noise. Without BIM data, it’s more difficult to identify and plan for potential safety hazards, increasing the risk of accidents and health issues.
The BIM-backed digital twin provides a detailed, accurate model of the building, including the location and type of materials used, which helps you identify potential safety hazards, such as the presence of hazardous materials, and plan mitigation strategies accordingly.
Avoid accidental damage with precise BIM data
BIM data can show the exact locations of HVAC, electrical wires, and plumbing inside the walls, helping ensure that teams don’t accidentally damage any of the other systems during the retrofit. This level of detail is invaluable for preventing costly mistakes and ensuring that the retrofit process runs smoothly.
For example, a large retail chain can use BIM data to map out the locations of electrical and plumbing systems in their stores. This allows construction teams to avoid cutting into walls or floors where these systems are present, reducing the risk of service interruptions and expensive repairs. Similarly, a government agency with multiple office buildings can use BIM to identify the precise locations of HVAC units, ensuring that retrofitting efforts do not disrupt critical climate control systems.
Create a bi-directional, continuous data loop with Tandem
The Autodesk Tandem® and Eptura™ integration improves building lifecycle management by bridging BIM and facility operations and maintenance workflows. It centralizes and structures BIM data, improving operational efficiency for data-driven decision-making and streamlined maintenance workflows. Tandem also ensures accurate and up-to-date information for retrofit projects, aiding effective budgeting and resource allocation. Tandem optimizes efficiency by providing visibility into energy consumption, enabling strategies to reduce environmental impact and lower operational costs.