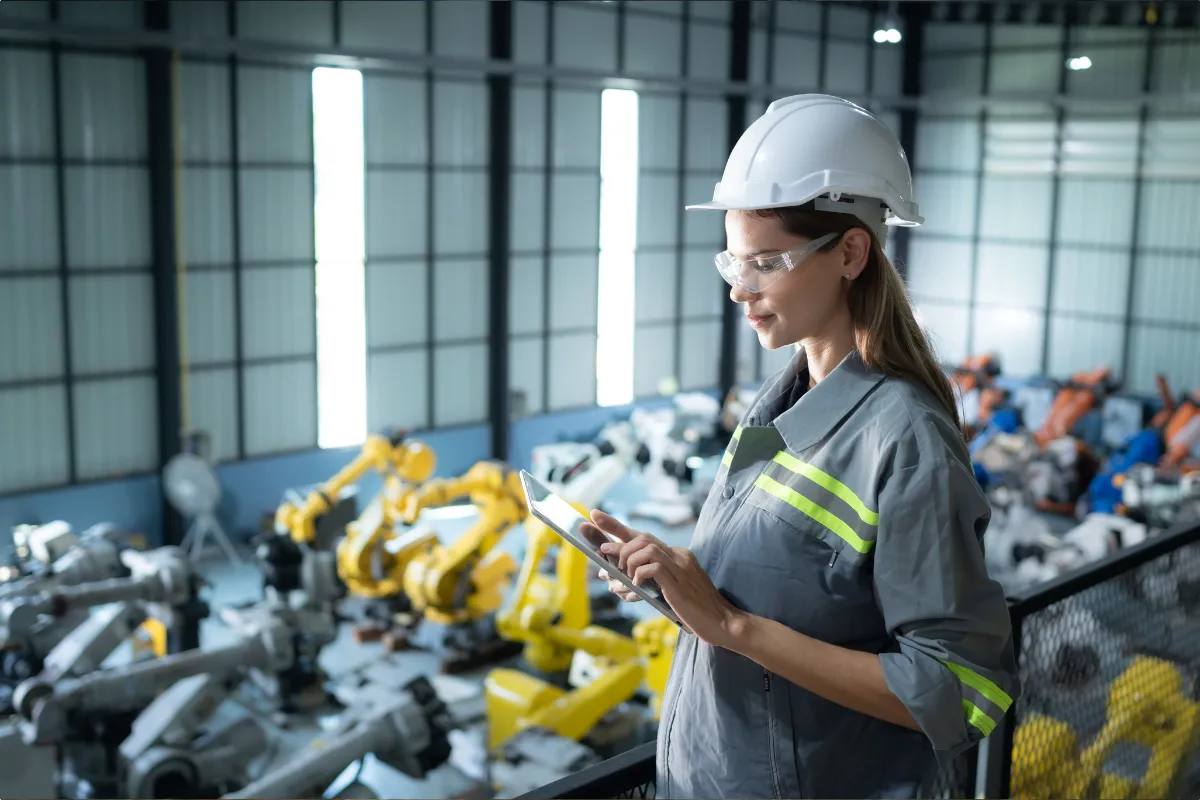
According to recent research by Eptura, on-demand work orders generally take twice as long as preventive maintenance. So, by finding and fixing small issues before they can become difficult problems, organizations can cut associated labor costs in half. But that data doesn’t exist in a vacuum.
By diving deeper into the reasons behind the numbers, facility and maintenance managers can more fully understand all the ways it pays to be proactive.
From there, they can better make the case to key stakeholders across the organization to increase investments in the programs that empower them to deliver more value at lower overall costs.
Eptura’s H1 2024 Workplace Index features proprietary research from enterprises in North America, Europe, and Asia Pacific, and leverages anonymous user data from over 5,000 companies, covering 19,000 buildings, 95.5 million desk bookings, and 25 million room bookings.
Time on reactive maintenance is double that of preventive maintenance
Eptura’s data shows that the more you can move to proactive maintenance, the more you can save on labor costs, because preventive maintenance work orders (PMs) take much less time. In fact, since October of 2023, our data consistently shows that maintenance departments spend on average roughly half as much time closing out PMs than they spend completing reactive work orders.
Even when the average time for reactive maintenance work drops, the time for preventive work does too, maintaining the previous difference. That means no matter how much better a team gets at reactive maintenance, they are still likely going to take half as much time when they work proactively.
The data makes simple sense. No matter how good you are at putting out fires, it’s always easier to prevent them. But it’s also important to look behind the numbers and understand all the different ways preventive maintenance takes less time.
Inspections and tasks are faster than unplanned fixes
For a combination of independent and interconnected reasons, in most cases a maintenance technician can close out a PM faster than an on-demand work order.
Less time waiting, more “time on wrench”
Planned and scheduled maintenance gives maintenance managers the time they need to work in various efficiencies. When maintenance technicians can decide when they will perform tasks and inspections, they can optimize based on proximity, for example.
If they’re already going to be in Building C on Wednesday looking at the air conditioning units, it makes sense to also schedule time to check the lights in the offices in that building. Instead of technicians going around in circles, they can move in straight lines.
They can also plan work in relation to production schedules and workplace occupancy trends. The maintenance team can schedule work on the conveyor belts during a planned stoppage, so they don’t have to worry about working between production runs and in between operators.
In an office, they can clean the air ducts on Friday afternoon, when they know there will be fewer people around.
For on-demand work orders, everything becomes less efficient. Zig-zagging between projects means technicians are often backtracking instead of making forward progress. And because they often arrive without knowing what tools, parts, and materials they’ll need, every trip between sites can include detours to grab supplies.
Little to no troubleshooting
On-demand work orders often require time-consuming diagnostics to identify the problem. Even something as seemingly simple as a stopped motor could be caused by a long list of possible issues, including:
- Overheating: Prolonged operation or insufficient cooling
- Electrical issues: Problems with the power supply, such as voltage fluctuations, phase imbalances, or power surges
- Mechanical failure: Worn-out bearings, broken shafts, or damaged gears
- Control circuit malfunction: Issues with the motor’s control circuit, such as a faulty start/stop switch, timer, or sensor
- Overload: Excessive current, leading to overheating
- Lack of lubrication: Insufficient lubrication, excessive friction and heat
- Contamination: Dirt, dust, moisture, or other contaminants inside internal components
The list is in no way exhaustive, and technicians might spend hours trying to diagnose why a machine has suddenly stopped working. With preventive maintenance, the techs know exactly what tasks need to be performed and can get straight to work without first having to figure out what to do.
In fact, the nature of preventive maintenance work means it is based on standardized procedures, with guidelines that technicians can follow, making the work more efficient.
For example, a technician follows a pre-approved set of steps and instructions for lubricating the conveyor belt rollers, which includes specific instructions on the type of lubricant to use and the amount to apply.
Less damage to deal with
The goal of preventive maintenance is to address potential issues before they become major problems. On-demand work orders are reactive, dealing with issues that have already caused disruptions, which can be more complex and time-consuming to resolve. It’s easier and takes less time to put out a small fire than one that has been left to grow.
So, for example, if during a PM a technician notices that one of the conveyor belts is slipping out of alignment, they adjust the belt before it breaks, preventing a potential production halt.
If the asset can move further along the p-f curve, an on-demand work order might involve replacing the entire belt and repairing all the damage it caused to the surrounding parts and even possibly other equipment when it snapped.
Preventive maintenance means more than just lower labor costs
Investing in preventive maintenance has many other advantages on top of saving on labor costs, including:
- Reduced equipment downtime: Preventive maintenance involves regular checks and the timely repair of equipment, helping identify potential issues early, minimizing the likelihood of equipment suddenly breaking down, which can disrupt operations and lead to costly emergency repairs and even more expensive production delays.
- Extended equipment life cycles: Regular maintenance ensures that equipment operates within its intended specifications, which reduces wear and tear over time. By routinely replacing parts that are prone to wear and keeping systems calibrated, preventive maintenance helps in avoiding the stress that can cause premature equipment failure.
- Improved energy efficiency: Equipment in poor condition tends to consume more power. Preventive maintenance ensures that equipment is running as efficiently as possible, which reduces energy costs — a major part of operating expenses in many facilities.
- Enhanced safety: Regular maintenance reduces the risk of accidents and malfunctions, which can cause injuries or worse, making it crucial for the safety of the employees and the financial well-being of the facility.
- Predictable budgeting: With preventive maintenance, facility managers can forecast maintenance costs and incorporate them into their budgeting process for better financial planning and resource allocation.
- Increased productivity: Equipment reliability is crucial for maintaining steady production rates and meeting delivery deadlines. Preventive maintenance ensures that machinery is always available and operational, avoiding the productivity losses that occur when equipment fails unexpectedly.
- Compliance with warranties: Many manufacturers stipulate regular maintenance as a condition of their warranty coverage. Failure to adhere to these stipulations can void warranties, leaving the facility responsible for the full cost of any repairs or replacements.
- Asset value retention: Well-maintained equipment retains its value better than equipment allowed to deteriorate. Equipment in good condition can command a higher resale value, turning what would be a depreciating asset into a more valuable investment.
Preventive maintenance also helps control inventory costs
By minimizing unexpected equipment failures, preventive maintenance reduces the need for a large inventory of materials and spare parts.
Facilities can save on the costs associated with purchasing and carrying these parts, as well as manage their inventory more efficiently. They have less money tied up in inventory, and they don’t have to worry about losing it to shrinkage, decay, or obsolescence.
A preventive maintenance program also allows for better negotiation with suppliers. With less urgency in replacing parts, facilities can wait for bulk purchase deals or negotiate lower prices with suppliers, further reducing costs.
For example, an automotive assembly line might use preventive maintenance to monitor and replace parts on their robots. Because they can predict when parts will need replacement, they can order parts in bulk when suppliers offer discounts, rather than making urgent, full-price purchases.
Companies also save on delivery costs. When inventory levels are tied to planned and scheduled PMs, a department might know months in advance when they will need specific inventory. They can then choose the most economical method of delivery.
Parts currently located across the country might travel mostly by rail or truck if the department doesn’t need them right away. But when unscheduled downtime means the maintenance department needs a specific part right away, rush delivery costs quickly rise. In many cases, the cost of shipping can be more than the cost of the part.
A modern, unified asset management platform helps set up and schedule preventive maintenance
Organizations hoping to find new efficiencies to cut operations and maintenance costs should look closely at how they can implement and then expand their PM programs. Eptura’s latest research proves that moving away from reactive maintenance has direct benefits on labor costs. But looking more closely, it’s clear there are even more benefits.
Implementing an effective PM program for a large variety of assets and equipment across multiple facilities and buildings requires a modern digital solution the empowers organization to safeguard and share data without worrying about introducing errors through manual methods.