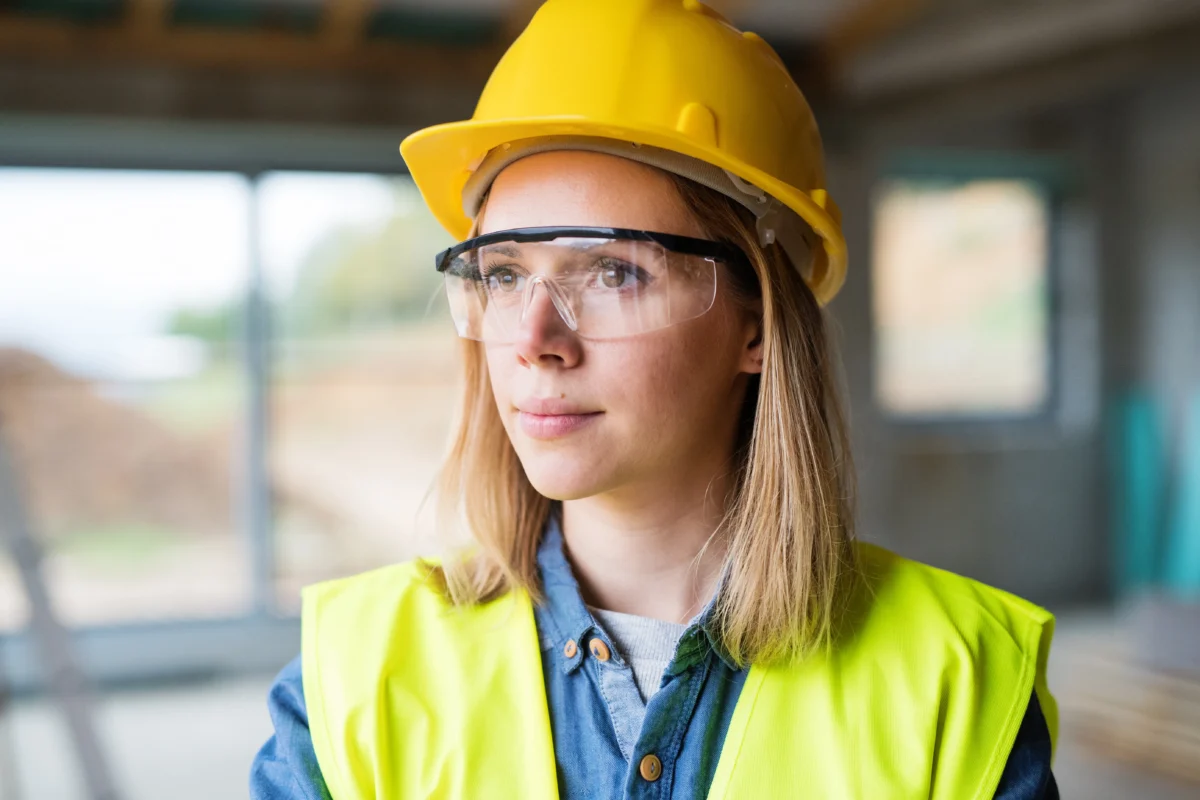
As construction projects grow in complexity and scale, the need for efficient and effective maintenance strategies increases exponentially. Even small delays caused by construction equipment downtime can throw a project off schedule, increasing a wide range of costs. With a comprehensive preventive maintenance (PM) program backed by a modern software solution, construction professionals can reduce the risks connected to breakdowns.
Why is equipment downtime so costly in construction?
Downtime equipment in construction is costly because of several interconnected factors.
Idle equipment leads to delayed project timelines, which can result in significant financial penalties and loss of reputation. Each day a project falls behind schedule can translate into extra costs for additional labor, material, and potential contractual fines.
The direct costs of repairing or replacing malfunctioning equipment can also be substantial. Unexpected breakdowns often require emergency repairs, which are typically more expensive than routine maintenance. Additionally, the cost of renting replacement equipment to keep the project on track can further add to expenses.
Equipment downtime disrupts the carefully planned workflow, leading to inefficiencies and reduced productivity. Remember, project management for construction generally follows the traditional waterfall model. Workers may be left idle, waiting for equipment to be repaired, which wastes valuable labor hours. This ripple effect can impact subsequent tasks, causing a domino effect of delays throughout the project.
And frequent downtime can negatively affect the lifespan of equipment, necessitating earlier replacements and increasing long-term capital expenditures. Regular preventive maintenance is crucial to mitigate these costs by identifying and addressing potential issues before they cause significant downtime. Minimizing equipment downtime isn’t just about saving money. It’s about ensuring the overall success and profitability of construction projects.
How can construction companies calculate the true cost of equipment downtime?
To calculate the cost of unscheduled downtime for equipment on a construction site, consider lost productivity, repair costs, and additional expenses such as rental equipment or overtime labor.
Lost productivity: Calculate the hourly output of the equipment and multiply by the hours of downtime.
Repair costs: Include parts, labor, and any diagnostic fees.
Additional expenses: Include rental equipment to replace the downed machine plus any overtime labor if workers need to catch up.
For example, a bulldozer moves 200 cubic yards of dirt per hour. If it’s down for eight hours, that’s 1,600 cubic yards not moved. Repairing the bulldozer costs $5,000 in parts and $3,000 in labor. And renting a replacement bulldozer costs $2,000 per day, and overtime labor is $1,500.
Lost productivity: 1,600 cubic yards at $2 per cubic yard = $3,200
Repair costs: $8,000
Additional expenses: $3,500
Total cost of unscheduled downtime: $3,200 + $8,000 + $3,500 = $14,700
This example is likely a best-case scenario for construction equipment downtime because it does not include the cost of the work delays between the first bulldozer breaking down and the replacement arriving. Once the work is off schedule, every other element of the project needs recalibration to meet an adjusted timeline. So, the rebar might now go in late, and the cement trucks might need to be rescheduled, too.
How can construction companies prevent unplanned downtime with preventive maintenance?
A PM program plays an important role in keeping construction equipment online, ensuring longevity, reliability, and cost-effectiveness. Regular inspections allow for early detection of issues, preventing minor problems from escalating into major failures that cause significant downtime. For example, checking a crane’s hydraulic system can identify leaks or worn hoses, which are inexpensive to fix but could lead to catastrophic failures.
Scheduled maintenance tasks, such as oil changes, filter replacements, and lubrication, keep equipment running smoothly and extend their lifespan. These tasks prevent excessive wear and tear, reducing the need for premature component replacements. For example, regularly changing the engine oil on an excavator can prolong engine life, saving thousands of dollars in potential repair or replacement costs.
A PM program can also improve safety on construction sites. Well-maintained equipment is less likely to malfunction, reducing the risk of accidents and injuries. Inspections also ensure that safety features, like backup alarms and emergency stops, are functioning correctly.
And well-documented maintenance records can increase resale value, providing a comprehensive history of the equipment’s condition and upkeep. In summary, preventive maintenance not only saves time and money but also promotes safety and preserves the value of construction equipment.
How does preventive maintenance software help construction companies prevent downtime?
PM software helps with streamlining processes and enhancing efficiency. Backed by the right solution, maintenance teams can:
- Eliminate complicated maintenance workflows: Automates scheduling, assigns tasks, and tracks progress, reducing manual effort and minimizing errors
- Retain valuable knowledge from senior techs: Captures institutional knowledge by documenting maintenance procedures and historical data, ensuring expertise is saved and shared
- Allocate resources seamlessly: Provides real-time visibility into equipment status and technician availability, enabling dynamic resource allocation and improved productivity
- Keep your entire team connected from anywhere: Offers mobile access, allowing field technicians to update work orders, access documentation, and communicate with the team remotely
- Unify your data into a single connected database: Centralizes equipment history, maintenance records, and inventory data, enabling informed decision-making and simplifying audits
By addressing these aspects, preventive maintenance software helps the maintenance team improve equipment reliability, reduce downtime, and increase operational efficiency.
What are the steps for implementing a PM program in construction?
Implementing a PM program requires a systematic approach that incorporates continuous improvement.
Assess current maintenance practices
Before implementing a preventive maintenance program, it’s important to understand your current maintenance practices. Conduct a thorough audit of your existing processes, equipment history, and failure patterns. Identify which assets are most critical to your operations and which are most prone to breakdowns. Also evaluate your current maintenance strategies, including reactive and preventive measures, to determine what’s working and what’s not. A thorough assessment helps you pinpoint areas that need improvement and set a baseline for measuring the success of your new program. Additionally, involve your maintenance team in this process to gather their insights and gain buy-in.
Implement a digital PM platform
A digital PM platform is the backbone of a modern, efficient maintenance program. Invest in a comprehensive software solution that helps you meet the specific needs of the construction industry. Key features to look for include:
- Equipment tracking
- Automated work order generation
- Maintenance scheduling
- Inventory management
- Real-time analytics
The platform should also offer mobile access, allowing technicians to update work orders and access documentation from the field. To ensure a smooth implementation, appoint a dedicated project manager, involve your information technology department, and look at following a phased rollout. Make sure there’s adequate training so all users are comfortable with the new system.
Develop a maintenance schedule
With your digital platform in place, the next step is to develop a maintenance schedule for your equipment. Start by gathering manufacturer recommendations for each asset, including inspection intervals, lubrication requirements, and component replacement schedules. Then, adjust these recommendations based on your equipment’s actual usage and operating conditions.
For example, equipment exposed to harsh environments may require more frequent maintenance. Input this schedule into your digital platform, which should automatically generate work orders based on meter readings or calendar intervals. Regularly review and update your maintenance schedules to ensure they remain relevant and effective.
Train the team
The success of your program hinges on the support and competence of your team. Provide comprehensive training on the new program, including the digital platform, maintenance schedules, and procedures. Ensure all stakeholders understand their roles and responsibilities, from technicians performing the maintenance tasks to operators reporting equipment issues, and management overseeing the program. It’s important to foster a culture of proactive maintenance, encouraging everyone to take ownership of equipment health. Regularly refresh this training to keep the program top of mind and update your team on any changes to the processes or software.
Monitor, analyze, and optimize
Continuous monitoring and analysis are essential to maximize the program’s benefits. Use your digital platform to track key performance indicators (KPIs) such as equipment downtime, mean time between failures (MTBF), and maintenance costs. Regularly review these metrics to identify trends, pinpoint problem areas, and measure the program’s effectiveness. Use this data to refine your maintenance strategies, optimize schedules, and improve procedures.
Encourage a cycle of continuous improvement, always looking for ways to improve equipment reliability and reduce maintenance costs. Regularly communicate the program’s successes and lessons learned to your team to maintain engagement and momentum.
It’s important to remember that with any maintenance program, implementing the right technology is only ever part of the solution. In an episode of the Asset Champion podcast, guest Cameron Christensen, CEFP, FMP, and Director of Asset Management for Facilities Operations at Princeton University, explains how technology is one piece of the puzzle.
“Technology is not the strategy. It’s an accelerator of strategy. It’s a very important piece of our strategy, but it’s not the strategy itself.”
How does a digital preventive maintenance platform help cut construction equipment downtime?
Implementing a modern PM platform helps streamline construction maintenance operations. By automating scheduling, assigning tasks, and tracking progress, the platform helps eliminate complicated workflows, reduces manual effort, and minimizes errors. It helps the maintenance team capture and preserve institutional knowledge from experienced technicians by documenting maintenance procedures and historical data, ensuring expertise is shared. And because it offers mobile access for field technicians to update work orders, access documentation, and communicate remotely, the entire team stays connected, boosting time on wrench and overall productivity.