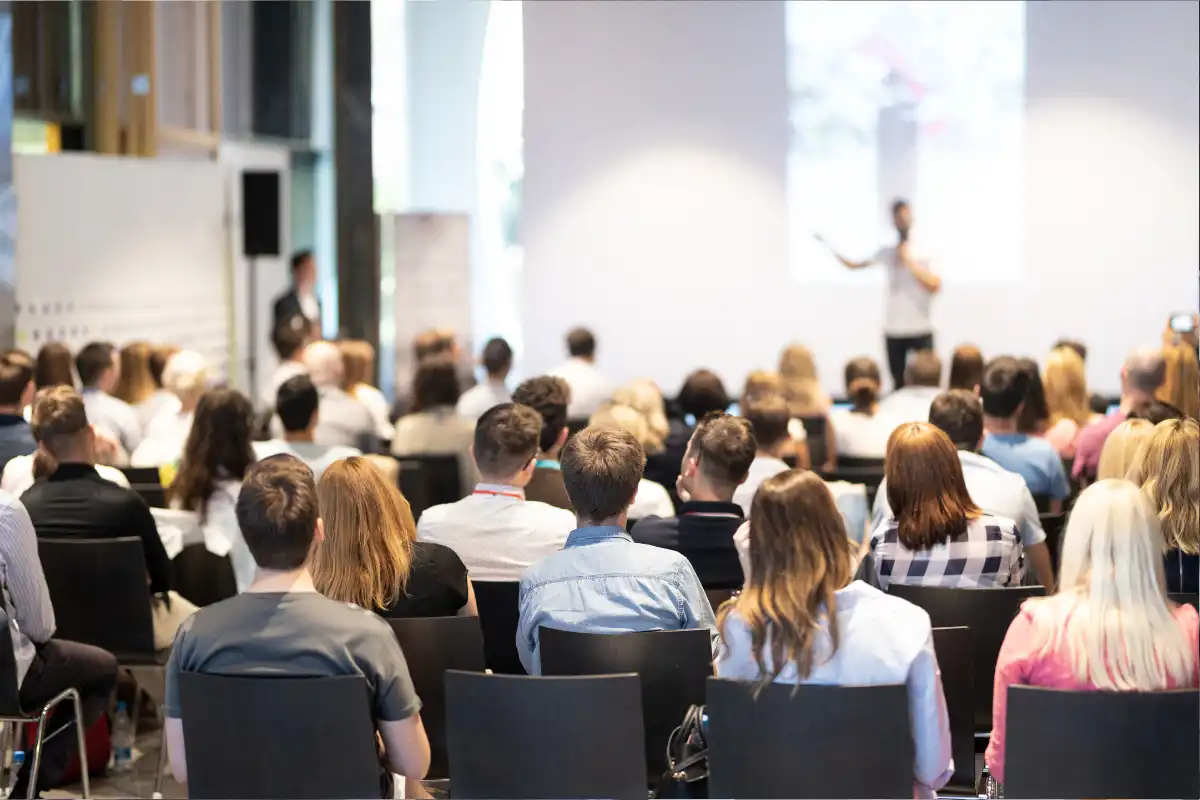
The stage is set, people have their tickets, and the big event is here. Hundreds of hours of hard work have all led to right now. Whether it’s one night or multiple days, the logistics for large-scale events is a complex combination of people, places, and supplies. Behind the scenes, the team must ensure that every element, from lighting to food service to waste management, operates seamlessly.
And as the scale and complexity of events grows, so does the need for advanced technology. Digital twins constructed with building information modeling (BIM) have emerged as pivotal tools in this arena, revolutionizing how venues host large-scale events.
What are BIM and digital twins?
BIM is an accurate, shareable, single source of truth that connects all teams on the project by incorporating multiple dimensions of data, including designs, materials, budgets, and timelines. Although traditionally implemented in the design and construction phases, owners and facility professionals are now leveraging new BIM-backed workflows later in the life cycle, in operations and maintenance.
Digital twins are accurate virtual copies of objects or systems, which you can then use to run simulations, track performance, and develop improvements. There’s a long tradition of digital twins in early-stage design and testing, but new applications include bi-directional flow of real-time data from facility management workflows. Facility managers can transform insights into operational efficiencies, improving everything from on-demand and preventive maintenance schedules to energy use.
Coordination between internal and external teams
Large events bring together many different vendors and suppliers. There’s the company that’s catering the VIP skybox and the concert merch vendors who need to set up stations at all the main entrances and exits. The team that sets up the stage needs to know how to get into the facilities and exact dimensions of the main hall and lines of site from the balcony. The security detail for the movie star at the comic convention asks for the precise location of the green room so they can control access. Even existing venue staff need help finding their way around, both during initial training and when transferring to new positions. On the most basic level, a digital twin built from BIM data is an accurate map of the venue that facility managers can share to help everyone get where they need to be.
In the case of an emergency during an event, facility managers can share relevant maps and real-time estimates on crowd sizes and locations with first responders, who can then better focus their efforts to protect people and property. Overseeing the evacuation of a facility is easier once you know roughly how many people are already inside and where they are in the buildings.
In the case of an asset or equipment failure that the onsite maintenance team cannot address along, the facility manager can use the twin to show third-party vendors the exact locations of everything from the pumps in the basement to the pipes in the walls.
Real-time monitoring and management
One of the most significant advantages of using BIM data to build digital twins is the ability to leverage real-time behavior for actionable insights. Digital twins offer a comprehensive big picture that stays in focus right down to the smallest detail of the venue’s operations, transforming how facility managers can oversee large-scale events. Imagine a convention center hosting a global trade show and conference with hundreds of thousands of attendees. A digital twin of the venue empowers facility managers to track crowd movement, identify congestion points, and monitor environmental factors like temperature and humidity. They can anticipate potential issues and deploy resources proactively.
For instance, Internet of Things (IoT) sensors placed in the main hall could detect a steady unpredicted rise in the ambient temperature, suggesting problems with the HVAC system. The maintenance crews could quickly find and fix any issues long before attendees notice. Or if pipe-mounted sensors detect a sudden spike in water use, technicians could pinpoint the likely location of the leak.
Other examples are more mundane but just as important to the smooth running of a large event. For example, venues can post QR codes in all the bathrooms that open the request portal from the facility management software connected to the digital twin, allowing everyone attending the event to quickly contact the maintenance or janitorial staff.
Energy management
In our earlier blog post in this series, we explored the connection between sustainability and big events. From lighting to sound systems to HVAC and catering, it takes a staggering amount of energy to host a big event. By providing actionable insights into current and predicted energy use, digital twins help facility managers to minimize environmental impact, while reducing costs.
These technologies help identify inefficiencies and implement tailored adjustments. For example, facility managers can feed weather data into a digital twin to generate accurate predictions for event-day HVAC load. And by adding data related to the lightshow at an upcoming concert, they can better prepare by scheduling inspections on all affected panels and breakers.
At facilities with multiple concurrent power-intensive events, the digital twin includes the various peak hours and energy consumption patterns, allowing facility managers to create a complex-wide smart grid that distributes power based on real-time demand, not a fixed schedule. Adaptive power management helps reduce wasted energy, cutting overall electricity costs, while ensuring that everyone has power.
Scenario testing and predictive maintenance
One of the most powerful applications of BIM and digital twins is scenario testing. By simulating various conditions within a virtual environment, facility managers can identify potential bottlenecks, safety hazards, and other logistical challenges before they occur. For instance, a digital twin can simulate different crowd sizes and densities to determine potential congestion points and assess alternate evacuation routes.
Another key benefit of digital twins is condition-based and predictive maintenance. Digital twins can be used to monitor equipment performance by tracking conditions like temperature, vibration, noise, and pressure. Facility managers can then use this data to identify potential equipment failures before they occur. This proactive approach to maintenance can prevent costly breakdowns and minimize unscheduled downtime, ensuring events run without minor inconveniences to major incidents.
The future of venue management is here
The integration of BIM-backed digital twins into facility management workflows is reshaping how operations and maintenance professionals host big events at large venues. By creating a dynamic real-time replica of a physical space, these technologies help facility managers to make data-driven decisions, optimizing resource allocation and mitigating risks.
The ability to test various scenarios and different strategies before implementing them is a game-changer. As the adoption of digital twins and BIM continues to grow, the industry can expect even greater advancements in operational efficiency, setting new standards for event management and sustainability in the future.