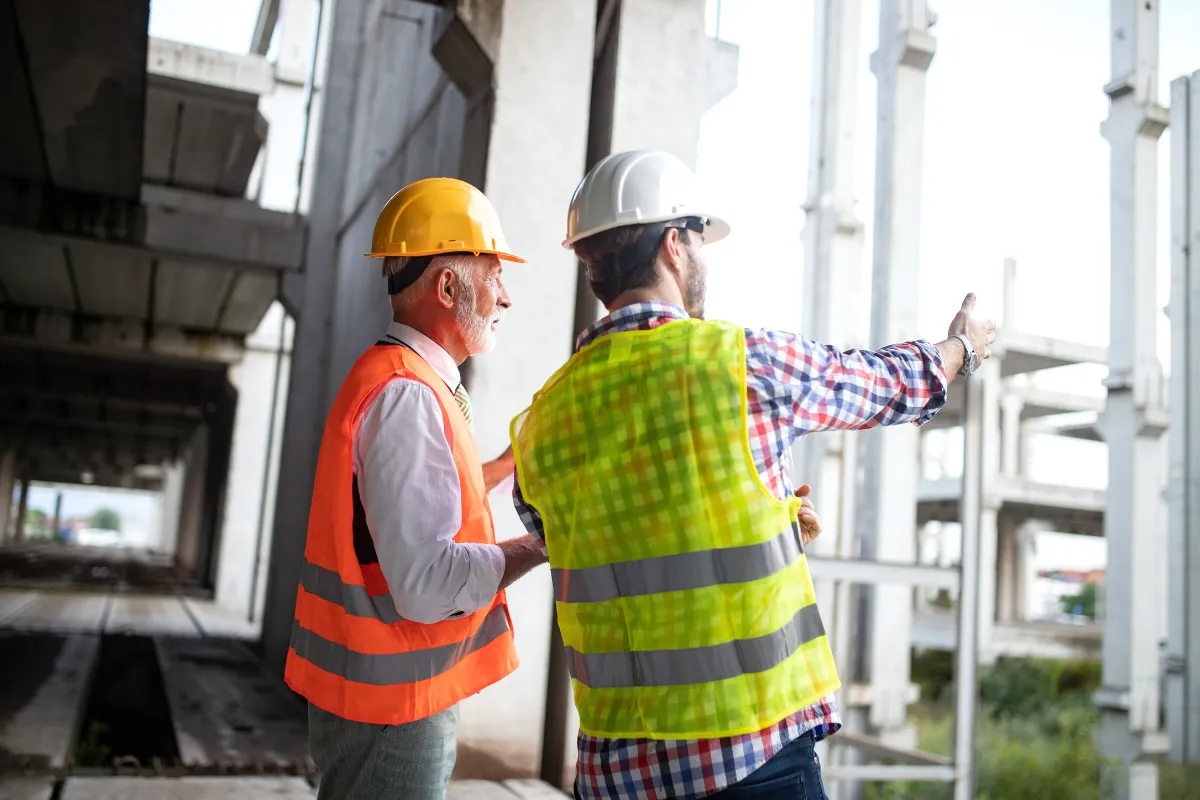
In industries reliant on skilled maintenance teams, the departure of experienced technicians can leave gaping holes in institutional knowledge, putting operations at risk. For large enterprises and facility managers, the challenge isn’t just about motivating teams but ensuring that critical expertise is passed on effectively from seasoned professionals to the next generation. As retirements accelerate and industries evolve with technological advancements, preserving and transferring tribal knowledge becomes a business imperative.
Here’s why institutional knowledge transfer is essential and how you can bridge the generational gap to safeguard operational continuity.
The clock is ticking: Why knowledge transfer matters
The risk of losing institutional knowledge
Institutional knowledge (sometimes called tribal knowledge) — unwritten, experience-based know-how — is invaluable.
It’s the nuanced understanding of processes, systems, and equipment that ensures smooth operations. When a senior team member retires or moves on, their departure often takes this expertise with them. For organizations heavily dependent on maintenance operations, this can lead to:
- Operational disruptions: Equipment downtime increases when no one knows the workaround or repair method a veteran might handle instinctively.
- Increased costs: Repair times lengthen, and mistakes multiply, leading to inflated maintenance budgets.
- Strategic vulnerability: Critical insights into systems and processes remain undocumented, leaving enterprises unprepared for unexpected challenges.
Key-person risk: A looming threat
When all critical knowledge resides in the minds of a single employee — or a few — it creates a “key-person risk.” If this individual becomes unavailable due to retirement, illness, or unexpected departure, the organization faces:
- Loss of expertise critical to daily operations.
- A steep learning curve for remaining staff to fill the void.
- Potential disruptions in standardizing processes.
Addressing this risk is not just about safeguarding knowledge — it’s about securing the enterprise’s future.
Building a bridge: Why mentorship and documentation are critical
Mentorship: A two-way exchange
Creating mentorship programs is one of the most effective ways to ensure knowledge transfer. Pairing senior technicians with younger team members fosters collaboration and mutual growth. While seasoned employees pass on their experience, younger technicians bring fresh perspectives and adaptability to new technologies.
Key benefits of mentorship include:
- Knowledge preservation: Seasoned employees can teach troubleshooting techniques, preventative maintenance strategies, and operational shortcuts that are often undocumented.
- Retention of younger talent: A mentorship culture shows junior staff that their growth is prioritized, improving engagement and reducing turnover.
- Improved adaptability: With ongoing dialogue, teams are better equipped to integrate new technologies while preserving legacy knowledge.
Standardizing processes
Standardization ensures that critical procedures don’t exist only in someone’s memory. By formalizing workflows and documenting key operations, organizations can reduce reliance on individuals and build a scalable model for knowledge sharing.
Steps to standardize processes:
- Audit existing workflows: Identify tasks heavily reliant on individual expertise.
- Document best practices: Work with senior staff to record their approach to problem-solving and maintenance tasks.
- Use visual aids: Develop diagrams, videos, and step-by-step guides to make complex processes more accessible.
- Create accessible repositories: Store all documentation in centralized digital platforms to ensure easy access.
Tactics for capturing and retaining institutional knowledge
1. Conduct knowledge audits
A knowledge audit helps identify the skills and insights at risk of being lost. Focus on:
- High-risk areas: Processes or equipment requiring specialized skills.
- Knowledge gaps: Areas where junior staff require training.
- Key contributions: Insights from senior staff that should be prioritized for documentation.
2. Leverage technology
Use modern tools to capture, store, and disseminate knowledge effectively:
- CMMS systems: Integrate a computerized maintenance management system (CMMS) to document procedures, track equipment history, and standardize tasks.
- Digital knowledge libraries: Build a shared repository of resources accessible to all team members.
- Wearable tech and AR: Equip technicians with augmented reality (AR) tools that overlay instructions and guides during repairs, combining senior expertise with modern innovation.
3. Establish structured training programs
Formal training programs should focus on bridging gaps between experienced and new team members. These programs can include:
- Job shadowing: Allow junior technicians to observe and learn from senior employees in real-world scenarios.
- Workshops and seminars: Offer regular sessions where senior staff can teach specific skills or share lessons learned over their careers.
- Scenario-based learning: Simulate common challenges to help younger staff apply theoretical knowledge under the guidance of experienced mentors.
4. Foster a knowledge-sharing culture
- Cultural buy-in is crucial. Create an environment where sharing expertise is rewarded, not seen as a threat to job security. Initiatives to consider:
- Recognition programs: Reward senior technicians who contribute to knowledge-sharing efforts.
- Collaborative tools: Implement tools like Slack, Microsoft Teams, or other platforms that encourage open communication and collaboration.
The role of technology in knowledge transfer
Industries are rapidly evolving, with technology driving much of the change. Senior technicians often have deep expertise in legacy systems, while younger staff may excel at adopting digital tools. Aligning these strengths ensures a smoother transition.
Digitizing legacy knowledge
Instead of letting tribal knowledge retire with senior staff, digitize it:
- Record video tutorials where experienced technicians demonstrate repairs or explain troubleshooting.
- Use mobile apps to create and share real-time updates on processes.
- Collect data from IoT-enabled devices to build predictive maintenance models.
Integrating AI and machine learning
AI tools can analyze historical maintenance data, providing insights that align senior expertise with emerging trends. This fusion of human experience and machine intelligence helps organizations future-proof their operations.
Benefits beyond continuity
The advantages of knowledge transfer go beyond simply filling gaps:
- Increased productivity: Teams equipped with institutional knowledge work more efficiently.
- Improved morale: Employees — both senior and junior — feel valued when their contributions and development are prioritized.
- Long-term scalability: With documented and standardized processes, scaling operations or onboarding new staff becomes more seamless.
Getting started: Strategies for leaders
- Identify champions: Select senior technicians willing to mentor and document their expertise.
- Invest in training infrastructure: Allocate resources for training programs, technology, and documentation tools.
- Set metrics: Measure the success of knowledge-transfer initiatives through reduced downtime, improved employee retention, or increased operational efficiency.
Passing the torch
As maintenance teams face the dual challenge of retiring expertise and evolving technologies, the need for effective knowledge transfer has never been greater. By fostering mentorship, documenting institutional knowledge, and embracing technology, large enterprises can bridge generational gaps and secure their future.
Facility managers and enterprise leaders must act now — before valuable institutional knowledge disappears. The clock is ticking, but with the right strategies, organizations can ensure that expertise is preserved, passed on, and leveraged for years to come.