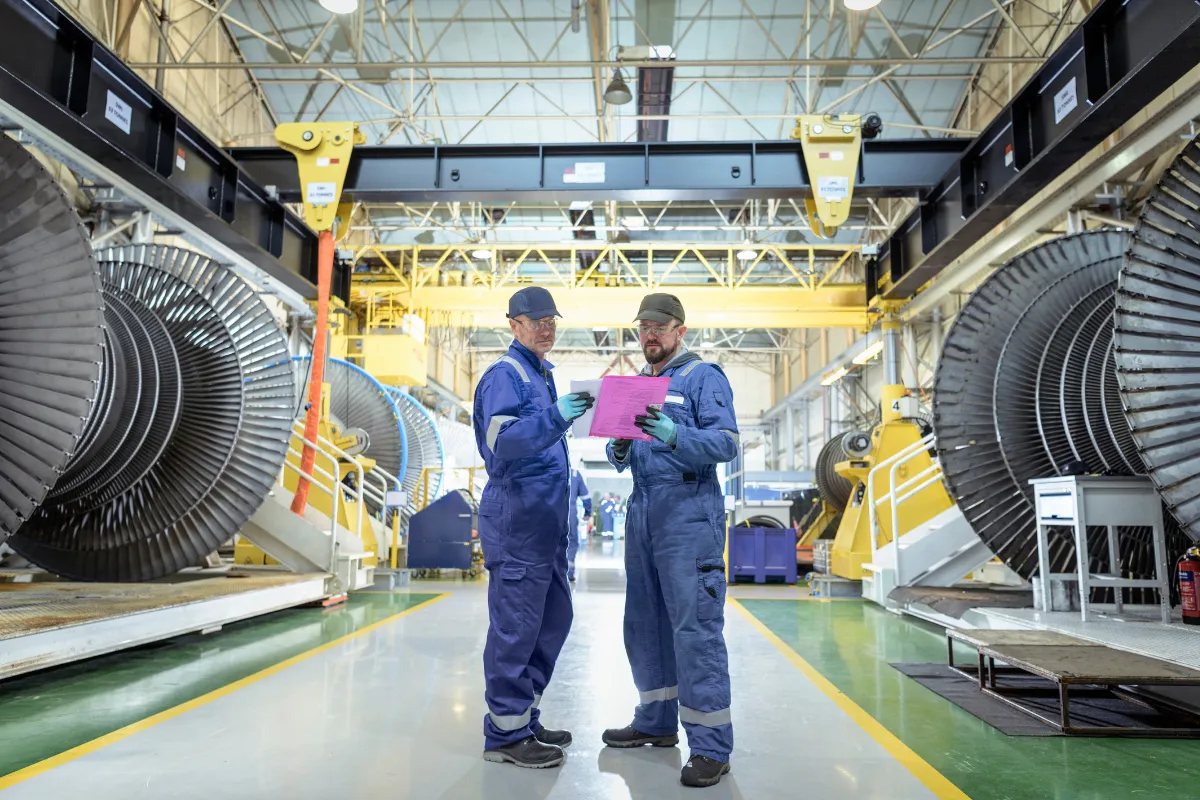
In large-scale operations like manufacturing, healthcare, and facilities management, efficiency is the foundation of success. When maintenance workflows are well-organized, teams can respond swiftly to repairs, keep equipment running smoothly, and prevent unnecessary costs.
For maintenance teams handling hundreds or even thousands of assets, a structured work order system ensures seamless coordination—technicians know exactly what needs attention, managers have clear visibility into progress, and maintenance tasks are prioritized effectively.
By adopting a centralized and automated approach to work order management, organizations can eliminate inefficiencies, streamline operations, and keep everything running at peak performance.
This is where a Computerized Maintenance Management System (CMMS) becomes a game-changer. By automating work order management, a CMMS eliminates guesswork, streamlines communication, and ensures that maintenance teams focus on the tasks that matter most.
Why traditional work order management falls short
Before modern maintenance software, work orders were often managed through spreadsheets, paper logs, or a mix of disconnected systems. While this approach may have worked when organizations were smaller and assets were fewer, it quickly falls apart as businesses scale.
A technician might receive a printed work order in the morning, only to find that the equipment issue has already been fixed — or worse, that a more urgent repair has come up, but they were never informed. Managers, on the other hand, spend hours manually tracking work progress, fielding calls, and trying to piece together maintenance records from scattered reports.
This lack of real-time visibility leads to miscommunication, delays, and missed opportunities to optimize maintenance schedules. Preventive maintenance tasks might be skipped or duplicated, parts might not be available when needed, and technicians end up responding reactively instead of proactively addressing issues before they escalate.
For organizations operating multiple facilities or managing complex machinery, these inefficiencies aren’t just frustrating — they’re costly.
The CMMS advantage: Bringing order to maintenance
A Computerized Maintenance Management System (CMMS) centralizes work order management, replacing fragmented processes with a streamlined, automated workflow. Instead of chasing down paper work orders or manually updating spreadsheets, maintenance teams can generate, track, and complete work orders digitally — all in real time.
One of the most immediate benefits of a CMMS is automated work order assignment. When an issue arises, the system automatically assigns the task to the appropriate technician based on availability, skill set, and location. This eliminates the back-and-forth of manually delegating tasks and ensures that work orders are addressed promptly.
In industries where uptime is critical — such as manufacturing, healthcare, and logistics — this kind of automation is invaluable. Instead of waiting for an asset to break down, teams can use preventive and predictive maintenance triggers to schedule repairs before failures occur. Equipment downtime is minimized, and maintenance teams can work proactively instead of reacting to emergencies.
Beyond work order tracking, a CMMS also improves inventory management. When a technician is assigned a task, the system cross-references spare part availability, preventing situations where repairs are delayed due to missing components. By maintaining accurate stock levels, facilities managers can reduce wasteful overstocking while ensuring that essential parts are always on hand when needed.
Improving accountability and compliance with CMMS
For businesses in regulated industries, maintenance documentation isn’t just about efficiency — it’s about compliance. Facilities need to keep detailed records of maintenance activities to meet industry standards, whether for safety regulations, equipment warranties, or government audits.
A CMMS provides a clear, time-stamped digital record of every work order, including who performed the task, when it was completed, and what parts were used. This level of tracking reduces liability risks, ensures regulatory compliance, and makes audits significantly easier.
Technicians no longer have to manually log completed tasks, and managers no longer need to sift through piles of paperwork to prove that maintenance was performed correctly. In high-stakes environments like hospitals, manufacturing plants, and energy facilities, this transparency is crucial.
The future of work order management: Data-driven and predictive
As technology continues to evolve, the role of CMMS in work order management will only grow more sophisticated. The integration of IoT sensors, AI-driven analytics, and mobile-first solutions is making maintenance smarter, faster, and more predictive than ever before.
IoT-enabled CMMS platforms can now detect anomalies in equipment performance — such as unusual vibrations or temperature fluctuations — and automatically generate work orders before failures occur. This means that instead of reacting to breakdowns, organizations can prevent them from happening altogether.
Mobile accessibility is another game-changer. With CMMS mobile apps, technicians can receive work orders, access asset histories, update job statuses, and even upload photos or notes — all from their smartphones or tablets. This ensures that maintenance teams stay connected, even in remote or large-scale facilities.
The future of work order management is no longer about just keeping up with repairs — it’s about creating a seamless, self-optimizing maintenance ecosystem that keeps businesses running smoothly.
Why CMMS is no longer optional
Today’s world moves quickly and is data-driven, so manual work order management is no longer a viable option for enterprises that want to stay competitive. The inefficiencies of outdated systems lead to rising costs, wasted time, and operational risks that no organization can afford.
A CMMS-backed work order management system changes the game by automating workflows, improving response times, and ensuring that maintenance efforts are data-driven and strategic.
Whether managing a single facility or a global portfolio of assets, the impact is undeniable: less downtime, reduced costs, and an operation that runs like a well-oiled machine.
The question isn’t whether organizations should invest in a CMMS — it’s how quickly they can implement one to start seeing the benefits.