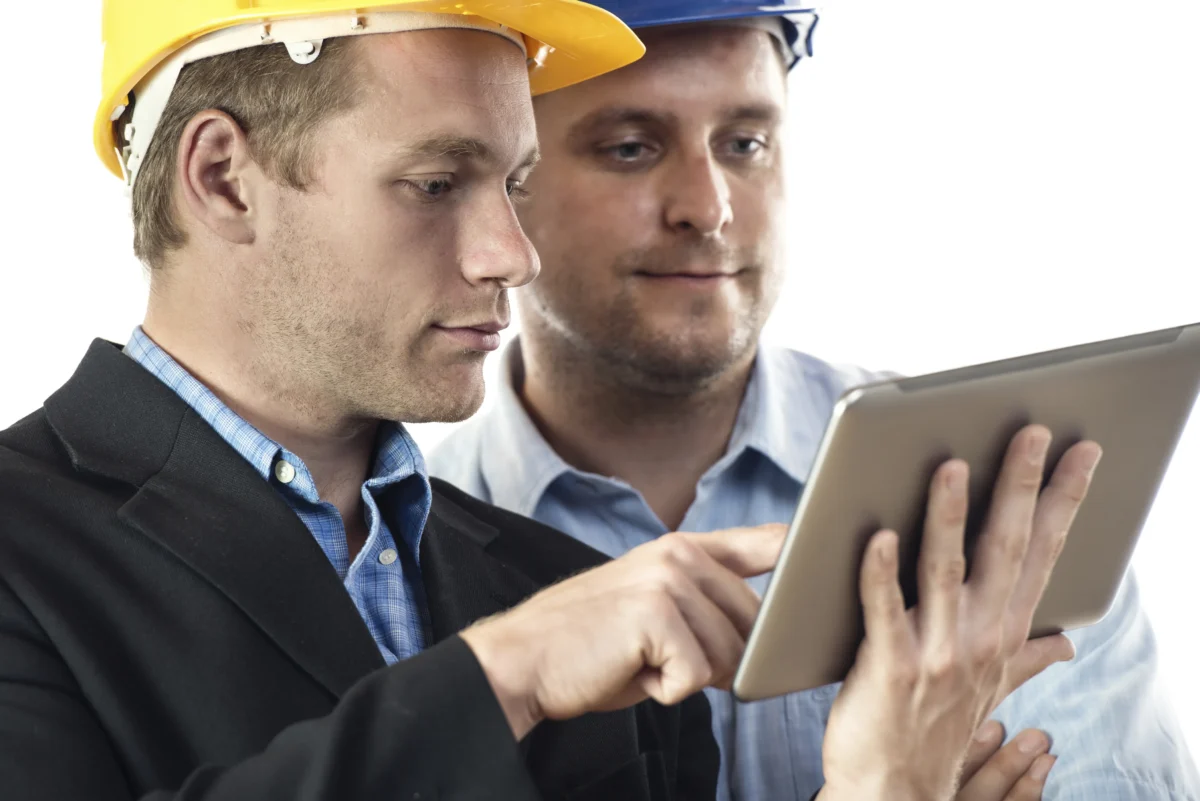
On some levels, there’s no practical difference between maintenance and repairs. They’re both tools you use to look after assets and equipment so they stay up and running.
But when you’re running a maintenance department and trying to get as much as possible out of your budget, there are important differences between the two, and the better you understand the role you need each to play, the easier it is for you to cut costly downtime.
A quick review of the definitions helps show how they’re sort of similar but also very different.
What are repairs?
One of the easiest ways to answer this question is to change the “what” to “when.”
Repairs are the work you do after assets or equipment fail, and although that might seem obvious, it is an important part of the definition.
Repairs come after failures.
And because failure is an important part of the definition of repairs, it’s worth looking at failure and all its nuances.
Partial failures
Most of the time, failures don’t go KABOOM. In fact, they can be even less dramatic than a screeching halt. A lot of failures are partial, which means the asset or equipment keeps on working, but it’s not working right.
So, imagine you have a machine that makes tin cans, and when it’s perfectly tuned, it can make 100 perfect tin cans every ten minutes. A partial failure could mean it’s making 100 cans but now takes 15 minutes. Or, every ten minutes, it’s able to make only 68 cans. Another type of failure might mean it’s making the right number of cans in the right amount of time, but a lot of them are imperfect.
Complete failures
Again, there’s doesn’t need to a be a KABOOM, but you’re more likely to see a screeching halt. With a complete failure, your asset or equipment stops working altogether.
This might sound worse than a partial failure, but it’s often better.
If you have a pool heater than partially fails, you might end up with a pool that’s only 75 degrees while 78 to 82 is ideal. Or it might heat the pool for only six hours of the scheduled eight. Here, a partial failure is more an inconvenience than anything else. But if your tin can machine partially fails, you might be producing a lot of imperfect tin cans without even knowing it.
Your machine doesn’t go KABOOM, but later on, your organization’s reputation might.
What is maintenance?
Again, we can answer the question more easily by changing that “what” to a “when.”
Maintenance is the work you do before assets and equipment fail. The reason you do it before the failures is because that allows you to avoid them as well as the associated repairs.
You can divide repairs by types of failures, and you can divide maintenance into different maintenance strategies, too:
- Preventive
- Corrective
- Predictive
- Condition-based
The differences between them come down to how you decide when to do the maintenance. So, for example, you schedule preventive maintenance inspections and tasks using a combination of manufacturers’ recommendations and asset maintenance and repairs histories. But with predictive, you use software to analyze a continuous stream of data pouring in from asset-mounted sensors.
But for all of them, it’s always the same idea that you complete the maintenance before failures as a way to avoid unscheduled downtime and costly repairs.
Which should you aim for, repairs or maintenance?
Maintenance is always better than repairs in the same way that an ounce of prevention is worth a pound of cure.
More cost
Repairs are always going to cost you more, and in more ways than you might think.
For example, a pump never gets lubrication and seizes. There’s the cost of the parts and labor to get it back online. But what if you don’t have the parts you need in inventory? Now you have to pay for a rush delivery on parts and materials. And what if the pump dies on the third shift? Instead of waiting for a tech to come in a repair it the next day, you have to call them in early, which means expensive overtime hours. Plus, the entire time that pump is offline, you have operators standing around waiting. Worst case, the whole line stops, wasting production time that the organization has to make up.
More stress
Just as stressful as working on assets with the whole production line standing around watching is sitting in your office waiting for disaster to strike.
It’s the same as watching a horror movie. The scariest part isn’t when the monster jumps out from the shadows; it’s before that, when you know the monster is going to jump out, but you don’t know exactly when.
When you move to maintenance and away from repairs, everything is cheaper and less stressful. Because you know when the inspections and work are scheduled to happen, there are no surprises. You can make sure you have the right people and parts in place because you know exactly when you need them.
How does a CMMS help you with repairs and maintenance?
Modern computerized maintenance management software (CMMS) helps at every step. At the center of it all is a database where you keep all your data safe, secure, and accessible. Integrated with that database are features for both on-demand and preventive maintenance.
Faster, longer-lasting repairs
Because repairs are an inevitable part of life, you need to find ways to get better at dealing with them. It’s the same as the fire department: they invest heavily in preventing fires, but that doesn’t mean they don’t have all kinds of tools and training for putting out fires when they happen.
With the right CMMS, you can control every aspect of on-demand work orders, from screening maintenance requests to generating, prioritizing, assigning, and tracking work orders packed with everything techs need to do the work right and close out fast. And because everyone on the team has access to the software from any mobile device, you can connect with everyone from everywhere.
Proactive, on-time maintenance
No matter how good you are at putting out fires, it’s always going to be easier to just prevent them from happening in the first place.
With the right CMMS, you can set up, schedule, and track a robust preventive maintenance program for all your critical assets and equipment, ensuring the team has the right combination of inspections and tasks to keep everything up and running.
And with the built-in reporting module, you can see exactly how well the team is following the schedule and which assets need more or maybe even less attention.
Next steps
Eptura’s here to help you get the solution that works best for you, from answering your questions about everything related to maintenance to helping you book a live software demo.
Summary
Although maintenance and repairs share the same goal, there are important differences between the two. The easiest way to see them is by looking at time: repairs are for after a failure, while maintenance happens before failures. For the maintenance team, it’s important to try to use maintenance to avoid repairs because repairs are more expensive, in multiple ways. And although, the team should be focused on preventive maintenance, they also need to good at on-demand repairs. Just like the fire department spends a lot of energy on prevention, they also have a lot of tools and training for fighting fires. Modern CMMS solutions help maintenance managers with repairs and maintenance. At the center is a database with all your data, safe, secure, and accessible. You can quickly manage on-demand work orders, while also running and tracking a robust maintenance program.