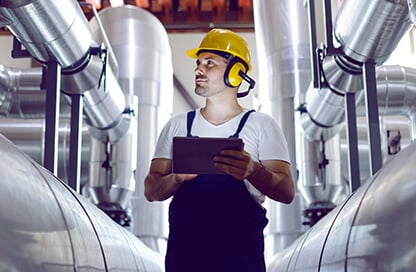
You want your facility maintenance team to complete their work on schedule and within budget. But you also want that work to be consistent and correct.
And that means you need facility inspection checklists powered by facility management software.
What is a facility inspection checklist?
It’s easier to understand when you see it in context. Preventive maintenance is the collection of scheduled tasks and inspections the maintenance department uses to find and fix small issues before they have a chance to develop into big, budget-busting problems. Each preventive maintenance work order is a PM.
The tasks are the things the team does during the PMs. They might adjust and realign a conveyor belt or change the oil in an engine.
The inspections are the things the team looks at before deciding if they should do anything. So, if the tech doesn’t find any leaks, they don’t fix the pipe. If the rollers on the garage door to the underground parking are rolling smoothly, they don’t adjust them.
A facility inspection checklist is a list of the things the tech needs to check so they can find issues early. For each item on the list, they mark it as either pass/fail or yes/no. When something fails, the tech sets up an on-demand work order to fix it.
What are the benefits of facility inspection checklists?
On the most basic level, it’s the same benefits you get from making a shopping list before you go to the grocery store. Even if you could trust yourself to remember everything you need to buy, it’s always easier to just bring a list.
And if you’re sending someone else to the store for you, that shopping list is an even better idea. Now you don’t have to waste time explaining to them what to get. And while they’re at the store, you don’t have to waste even more time worrying about what they’re forgetting.
There are also benefits more specific to facility maintenance, and most of them are the direct results of standardizing your inspections. There are a lot of benefits when everyone is doing everything the same way.
Better consistency and planning
Once you have your inspection checklists set up, you can count on two things.
One: The maintenance team is doing the inspections properly. The techs aren’t accidentally skipping or missing anything. No one is forgetting anything.
Two: Because everyone is doing everything the same way, the PM should always take roughly the same amount of time, which is a big help when you’re trying to schedule work.
If you know techs need about X minutes to run through an inspection checklist, you can schedule Y number of inspection PMs to a tech, knowing they can close them all out no later than time Z.
Stronger troubleshooting
Later, if things go wrong and an asset fails, it’s easier to troubleshoot the problem because you’re working with fewer variables.
When every tech has their own version of an inspection, you have no real idea of what they’re checking or what they consider important enough to fix. Here, when an asset fails, you don’t know what was going on prior to the problem.
But when every tech’s work is interchangeable with every other tech’s work, you don’t have make as many guesses.
Faster training
Although almost every trade has a long and proud history of apprenticeships, where someone with a lot of experience in a trade brings on an apprentice who does unskilled work in exchange for training. But for a modern facility maintenance team, this system tends to slow things down, pulling experienced techs away from critical jobs so they can get the new techs up to speed.
When you have all your inspections standardized into checklists, junior techs can start working independently from Day One.
What should you include in an inspection checklist?
You should include everything your techs need to do the inspections correctly, including what to bring, what to avoid, and what to do.
What to bring
Here, you can include the tools they need to complete the inspection. In a lot of cases, it’s just visual inspections. For example, techs need to look for leaks by checking for puddles under assets. Need to know if your car has an oil leak? Look for oil stains on your parking spot.
But for some inspections, for example inspections related to leak detection and repair (LDAR), techs need sophisticated portable sensors. For others, they need specific personal protection equipment (PPE).
What to avoid
On the theme of personal protection, your checklist should include information on any safety concerns. For example, what to avoid touching when doing the inspections, what PPE to use, and how to correctly lock out and tag out the assets and equipment.
What to do
Once the tech has everything they need and is aware of and ready for any safety issues, they need to know what to inspect and how to recognize issues. For example, an inspection checklist for a furnace includes information on where heat should and should not be escaping.
Now that you know what you need to include in an inspection checklist, let’s look at the specific steps you need to make the checklists.
What are the steps for writing a facility inspection checklist?
Your checklists must follow a specific order, so it makes sense that the process of creating them also has a set order.
Collect existing asset documentation
Start by getting your hands on as much official information as you can on your asset or piece of equipment. If you want to make an inspection checklist for the forklift, get the owner’s and OEM manuals. Keep in mind that you want the latest documentation, and that might mean reaching out to the manufacturer and asking if there’s been any recalls or updates.
Look at the maintenance and repairs histories
Who knows you better, your mom or your spouse? It depends on how long you’ve been married. At first, your mom knows you best. But after a long marriage, your spouse is the expert.
It’s the same with your assets and equipment. Those manufacturers’ documents are from back when the people who designed and made the assets knew them best.
But it’s likely been a while, and by looking at the maintenance and repair histories, you can get a better idea of what to include in the checklists.
Get advice from your senior maintenance techs
Continuing with the theme of direct knowledge, make sure to talk with the technicians who have been working directly on your assets.
They’re the assets’ “spouse,” and there’s a good chance no one knows the assets better.
Once you’ve hammered out what to include on the checklists, it’s time to focus on making each item as clear and concise as possible.
And yes, spelling counts.
Which grammar rules do you need to follow for checklists?
Did you catch the grammar glitch in the subhead? It should be “what,” not “which,” which you use when there is a predetermined number of items to choose from.
Are you now worried about that last sentence because it ends with “from,” a preposition? Should it be “from which to choose”? And “last sentence” is also wrong, right? Shouldn’t it be “previous sentence”?
Don’t fall down the rabbit’s hole (Rabbit’s Hole?) of second guessing everything you write. Focus on communicating important information in the most direct ways possible.
Here are some quick tips for writing good checklists.
Use imperatives or yes/no questions
You can start each item on your checklist with an imperative. Here are some good ones:
- Check
- Inspect
- Compare
- Examine
- Confirm
You can also go with yes/no questions, including:
- Are …?
- Is …?
- Do …?
Use concise language
Regardless of the structure you choose, be concise.
A lot of your items can start with “check,” but when you can, try to be more specific. In some cases, checking means visually inspecting. In others, the maintenance tech needs to touch the asset. So, instead of “check,” it might make more sense to use “visually inspect” or “confirm.”
Be concise when talking about assets, especially when there are a group of identical ones close together. For example, when writing a checklist for an air conditioning unit, make sure you explain exactly which of the ten units in a row on the roof you mean.
A big benefit of concise writing is that it’s nice and short. And the last thing you want to be is long-winded. Remember, if things are too long, you run the risk of technicians pencil whipping their way down the list. Include everything techs need. Leave out everything else.
Be consistent
If you’re going with questions, stick with them. Prefer imperatives? Try to write everything in the imperative form.
And try to be consistent in how you want the techs to answer yes or no if you’re using questions.
Is there water or any other liquid pooling under the asset? yes/no
Does the garage door to the underground parking move smoothly both up and down? yes/no
See the problem? In the first item, answering yes means the tech should generate an on-demand work order to fix the issue. But in the second item, answering yes means everything’s working, and the tech can move on to the next item on the list.
Switching back and forth between yes meaning something is wrong and yes meaning everything is fine creates just a little bit more mental work for your techs, distracting them right when you need them to be laser focused on inspecting the assets.
How does facility management software make checklist templates easier?
Modern facility management solutions makes life easier because it simplifies capturing data, keeping it safe, and making it accessible.
The reason is because your data lives in one central database in the cloud. Anytime anyone on the maintenance team updates the data, those changes are reflected in real time.
Once you’ve hammered out your checklists, you can save each one inside a work order template. When you need to generate a new PM or work order with that checklist, you can copy over your work with just a few clicks.
Later, if you want to go back and update your checklists, you only need to make the changes once to the template. Then every time you use that template moving forward, it has all your updates.
You never have to worry about making changes to a bunch of loose pieces of paper or spread-out spreadsheets.
Summary
Facility inspection checklists are an important part of an efficient preventive maintenance program that cuts costs by finding and fixing small issues before they have a chance to grow into problems that cost the organization time and money.
By standardizing the inspection process, a facility manager gets better, more consistent work out of the maintenance team, making it easier to schedule resources, troubleshoot when assets or equipment fail, and even train new techs. There are specific steps the FM can follow to write good checklists, but an important part of the process is adopting modern facility management software. With the software solution, your FM can easily share and fine-tune the checklists, ensuring techs have easy access to up-to-date help.